With aerospace brazing and aerospace soldering, the joint is effected by inserting a metal between the two metal surfaces being joined, the inserted metal having a lower melting point than that of the materials being joined. With fusion welding, the joint is effected directly between the parts being joined by the application of heat to melt the interfaces and so cause the materials to fuse together. Aerospace fusion welding thus requires the melting point of the components to be exceeded. With solid-state welding, the joint is effected by applying pressure to bring the interfaces of the joint materials into intimate contact and so fuse the two together. Ductile materials such as copper or aluminium can be joined by this method at room temperature. Most materials, however, require heat to render them sufficiently ductile.
Aerospace welding processes are capable of producing high-strength joints. The temperatures involved in making the welds may, however, cause detrimental changes in the materials being joined. These may be local distortions due to uneven thermal expansion, residual stresses, or micro-structural changes.
Micro Soldering Iron
Welding processes
There are four main types of process used for fusion welding:
Electric arc welding
With electric arc welding, an arc is produced between the workpiece and an electrode. When the arc is struck, the tip of the electrode melts and globules of it are projected across onto the joint. Temperatures of the order of 20 000 K are produced with currents between the electrode and workpiece of the order of 200 A. Most electrodes are coated with a flux which vaporises and provides a protective shield to reduce oxidation of the molten metal. An alternative method of providing such shielding is to use a gas-shielded arc in which an inert gas is directed over the weld pool. Arc welding gives high quality welds, is a flexible method, and is low in cost. It is used for strong joints.
Electrical resistance welding
With electrical resistance heating, the high temperatures necessary for welding are produced by passing an electric current across the interface of the joint and producing resistance heating in the electrical resistance of the joint. Electrical resistance welding can be used to give butt welds between two surfaces which butt up to each other, seam welds (a line of welded material between two sheets) or spot welds in which the weld occurs on just small regions, the spots. Spot welding is used for seam welding in sheet metal fabrication.
Radiation welding
With radiation heating, the high temperatures occur as the a result of focusing a beam of electrons, in a vacuum or low pressure, onto the joint area. This method can make deep narrow welds. An alternative is to use a laser to focus a beam of radiant energy onto the joint. This does not require a vacuum chamber.
Thermochemical welding
Thermochemical welding uses a chemical reaction to generate heat. Also used is oxygen and some fuel gas such as acetylene combining in a flame. A filler rod is used to provide extra metal for the joint. Called Thermit welding, it is used for the repair of iron and steel castings, railway lines, shafts etc
Pressure welding
This involves a ductile material being pressed against a similar or dissimilar metal; aluminium and copper can be welded at room temperature by this method. This is used for cladding sheets with a thin layer of some other metal e.g. aluminium alloy sheets are often clad with aluminium to improve corrosion resistance.
Friction welding
This involves sliding one material surface, under pressure, over the other. The friction breaks up any surface films and softens the surfaces by virtue of the rise in temperature produced by the friction.
Explosive welding
With explosive welding, the two surfaces are impacted together by an explosive charge.
Special Price!!! TEKTON 7266 30-Watt Soldering Iron
Click for larger image and other views
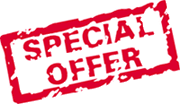
TEKTON 7266 30-Watt Soldering Iron Feature
- Insulated Pencil-Type Polymer Handle
- Replaceable Nickel Plated Tip
- UL Listed
- Complete with Tip Stand
- General-Purpose Soldering Iron for Electronics Repair, Wiring Connections, Automotive Electrical System Repairs, and Circuit Boards
TEKTON 7266 30-Watt Soldering Iron Overview
MIT 30-WATT SOLDERING IRON features: Operates at 30-Watts Using 110-120 Volts, Insulated Pencil-Type Polymer Handle, Replaceable Nickel Plated Tip Heats to 700 degree, 5-1/2 Ft. Power Cord, UL Listed, Complete with Tip Stand, Use for Any Fine Soldering Project Including Electronic Repair, Speaker Connections, Computer Repairs, Hobbies, ect.SAVE NOW on the special offers below!
Available In Stock. |
This TEKTON 7266 30-Watt Soldering Iron ships for FREE with Super Saver Shipping. |
Price : Click to Check Update Prices Please. |
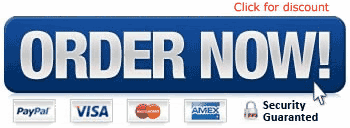